I
Concept/Architecture
Optimization for Low-Cost Products
with 2 examples: Electronic Architecture
and Large Frame Structures
by Dr. David M. Anderson, P.E., CMC
© 2021
Fellow, American Society of Mechanical Engineers
Many designs will work; only one will be the lowest cost!
New
article:
Stopping counter-productive policies before change can start
PREREQUISITES
A) Product cost must be computed based on
Total Cost
that quantifies all costs, including overhead costs, and rationally
allocates all appropriate costs to every product variation.
1) Total cost measurement complies all the cost for every product
variation that, when subtracted from the selling price, yields the true profit,
which is the only way to compute realistic profitability. Being able to
sort all product variations by true profitability can provide:
• an objective basis for
product portfolio planning
that will prioritize resources based on developing products with highest
expected return from given resources.
• an objective basis for
rationalizing away money-losing products
2) Total Cost encourages behavior that actually minimizes total
cost – meaning all costs.
3) Without total cost, new product development efforts are in danger of
being compromised and penalized in three ways:
• Product development resources may be diluted pursuing too
many products that may all appear equally rewarding, which is
statistically unlikely. On the other hand, total cost measurements will
better estimate profitability, thus enabling development efforts to be
prioritized on only the highest return efforts
• Resources may be drained away from product development teams to build
unprofitable existing products that true profitability metrics should
have been identified and rationalized away.
• When the new product is launched, it will have to pay a loser tax to
subsidize all the unprofitable products, thus raising the new product’s
selling price, which, in turn, will make it less competitive.
For more on Product Line Rationalization, see the
summary
article on Rationalization or the full chapter (Appendix A) in the
book Design for Manufacturability & Concurrent
Engineering
B) Avoid counterproductive policies that inhibit or thwart good product
development such as overloading Engineering with low-profit new development
projects, “taking all orders” and “accepting all customizations” for existing
product variations, deadline “management” (which can be counterproductive if
poorly set deadlines don’t encourage thorough up-front work), not quantifying
total cost,
trying to remove cost after the product is designed,
low-bidding on custom
parts, and
offshoring to “save cost,” which prevents Engineering working together with
Manufacturing (concurrent engineering). See Ortho World's summary :
"Why Offshoring Manufacturing 'To Save Cost' Won’t, but Trying May Compromise
Product Development, Delivery and Quality" at
https://www.orthoworld.com/index.php/publications/view_article/221614
After DFM training, one large company that had pioneered many of these, needed
to launch an initiative called "DFM vs policy" to correct current
counterproductive policies for their first product development team to utilize
these new methodologies.
HOW TO DEVELOP PRODUCTS THAT
EXCEED COST GOALS
The following methodologies are presented in order of most effective first. For
ambitious cost goals, all must be employed:
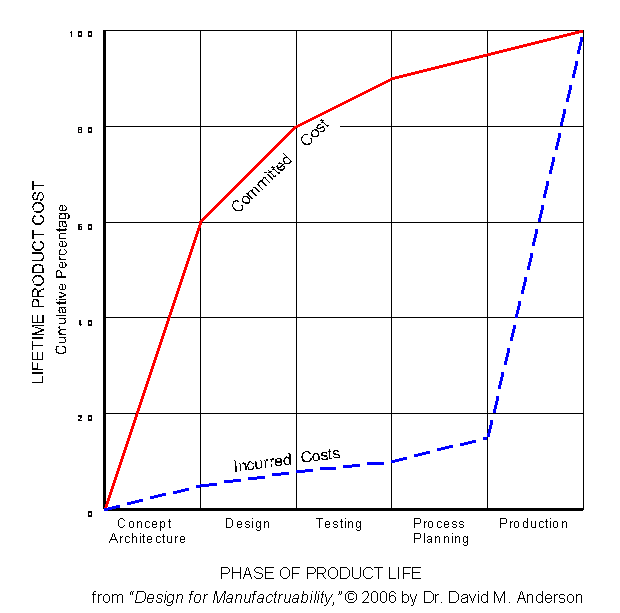
1) How to achieve cost goals with concept simplification and breakthrough concepts
for major cost goals.
Since the concept stage determines 60% of cost concept simplification is important for modest cost goals,
whereas breakthrough concepts are essential for major cost goals. Here are two
examples of concept optimization, one electrical and one structural, that show
examples of applicable breakthroughs. All these methodologies are presented in
Dr. Anderson’s seminars and explored in his workshops.
For Electronic Products
• Base the architecture on high levels of silicon
integration, either off-the-shelf (VLSI, FPGAs, etc.), custom silicon (ASICs),
or programmable off-the-shelf silicon (like FPGAs). These chips combine may
functions into dense “integrated” chips, thus replacing many “discrete”
chips. This can minimize assembly steps, lower placement assembly charges,
reduce material overhead costs, and lower quality costs (next numbered
topic).
• A breakthrough concept would be past the threshold
after which circuitry could be condensed to fit on a single printed
circuit board (PCB).
• Minimize inter-board wiring complications to reduce
assembly cost and lower quality costs, which are both very high for hand
soldered wires. At the minimum, multiple circuit boards should plug
directly together with all connectors automatically placed and soldered.
• One breakthrough concept would raise the silicon
integration to condense electronics to a single PCB that would eliminate
the need for inter-board connections.
• Another breakthrough concept would be to connect multiple circuit
boards with flex layers which are insulated flexible traces
that are actual layers on all circuit boards so that all signals
flow through traces that are automatically soldered to all components in
the circuit without any mechanical connections. This eliminates
many performance and quality variables, which lowers product development
expenses, minimizes launch delays, and reduces quality costs and
reliability liabilities.
These flexible traces can also be automatically soldered to
non-board-mounted components such as switches, controls, displays,
antennas, and connectors to other subassemblies.
• Minimize expensive, low-quality, unreliable
connections, such as those made by hand soldering or wiring lugs to
terminal blocks, both of which require skill and have a high potential for
errors and mistakes. At the minimum, wiring lugs screwed into terminal
blocks could be replaced by connectors and cables, hopefully standard and
available off-the-shelf.
• A breakthrough concept would be an architecture that is based on pairs of
standard connectors coupled together with off-the-shelf cables. For
instance, for up to 9 wires, use a standard DIN “serial” cable; for coaxial
wiring, use standard coax connectors and off-the-shelf coax cables. Thus,
multiple pairs of off-the-shelf cables would replace very expensive wiring
harnesses that are made by hand, usually using “tooling” that consists of a
plywood sheet with wire paths indicated by back marker lines between nails,
which can easily lead to mistakes and poor quality joints.
Such standard connectors would be designed into circuit boards, connector
panels, and specified for connected devices (with “extra” space provided by
higher levels of silicon integration, more compact components, and more
space-efficient circuits).
• Minimize the cost of configurations and variety
• A breakthrough concept would be to strive for the
maximum configurability done programmably.
• Another breakthrough concept would be an architecture based on common,
versatile bare circuit boards, onto which various sets of components are
automatically placed and soldered as needed. Note that all PCB assembly
machine tools are CNC programmable machine tools, but most are use in a
batch mode.
• Use modular design to reduce development effort, save
cost, and improve quality. At the minimum, companies can reuse their own
proven modules that can be assembled by plugging them into to common
interfaces.
• A breakthrough concept would be to design the
architecture to include interfaces to accept standard off-the-shelf
modules, such as PC boards for processing, memory, control,
input/output, power management, and other standard functions.
• Another breakthrough concept would be structure families of products
(product platforms) around an architecture that allows maximum
proportion of pre-written software modules that can be combined for a
wide range of product variations. The strategy would modularize software
code into objects with a well defined programming interface, which will:
• Minimize software development costs with broad
reuse of modules for subsequent, derivative products/variations, and
parallel products in a product family.
• Minimize new code writing with the maximum reuse of software
modules.
• Systematically eliminate bugs, by thoroughly debugging modules and
then reusing the debugged modules – This is HP’s debugging strategy
for non-patchable products. This strategy depends on allowing no
changes or modifications to debugged modules, unless a new round of
writing new code and debugging is warranted.
For Large Structures
• Avoid large weldments that are hard to manufacture.
Large weldments require much skilled labor to make and expensive large
machine tools to machine all the features and mounting holes after welding.
With the possible exception of large pressure vessels that must be
monolithic, large welded structures incur the following costs that
can greatly be reduced:
• high-skill labor cost to weld plus other labor to
position, fixture, straighten warpage, and grind.
• the cost and delays for annealing the weldments or the risk of
fractures from residual stresses.
• the imprecise and labor intensive practice of mounting parts in slots
or large holes and then aligning them manually.
• machining large parts after welding, which may require large machine
tools and furnaces to anneal them, which (a) are very expensive to buy
or have high hourly charges to outsource, (b) usually involve
labor-intensive on-line setups which adds more time to expensive machine
charges and increase the build time, and (c) may involve transportation
and queuing delays.
Similarly, large castings are expensive to cast after
lengthy setups plus the molds/dies are expensive and their construction may
incur long lead times.
• A breakthrough concept would be to avoid or replace
these with assemblies of parts that are manufactured automatically on
affordable CNC machine tools and assembled precisely and rigidly by
various DFM techniques as presented in the
Workshop for Reducing Cost and
Material Usage for Large Parts.
• An alternative would be go initiate independent design studies to
generate promising approaches for the company to evaluate, select, and
implement. Given his experience both welding and machining, Dr. Anderson
is particularly effective for complex parts that could benefit from very
manufacturable design concepts and concurrently engineered low-cost
processing.
Relevant
sections from the 2020 DFM book:
3.3.9) Concept breakthroughs, that are pivotal for innovation will
be missed, if the project time-lines do not provide time for "thorough up front
work," as shown in the lower time-lines in both graphs in
http://www.design4manufacturability.com/half-the-time.htm
Example: in the
concept breakthrough article, one category of concept breakthrough is for electronics, including higher
levels of electronic integration, combining circuit boards, and simplifying
inter-board wiring could be discouraged if (a) the status quo is using
‘free” wires and under-reported assembly labor and quality problems and (b)
the solutions appear as expensive new BOM entries without quantifying all
the cost and throughput benefits. See DFM book
Section 3.3.
3.8.4)
Inventory costs
can easily exceed profits. Without standardization, all delivered parts will
go into “raw materials” inventory, which will then be kitted for each
production batch, thus creating a lot of Work-In-Process inventory, and then
wait as Finished-Goods inventory until shipped. Inventory carrying cost
actually costs a quarter of its value per year (see plot in the
Mass Production article), and can be eliminated by
designing for lean production and build-to-order, which will not be
possible with all the above consequences of defining cost as primarily based
on part cost. See DFM book Section 3.8,
Breakthrough concept principles
for All Products
• Look for breakthrough concepts for new products
on a clean-sheet-of-paper premise, even if constraints are not that
open. The premise will help generate many ideas that might encourage such a
venture and, even if not, some ideas may be applicable to less ambitious
projects.
• Look for breakthrough concepts for much better modules or subassemblies
that can become backward-compatible replacements on existing products and
then become the basis for new designs – this is the premise of the
Workshop to Reduce Cost and Steel
Usage.
• Arrange customized Product Specific
Workshops for important product development projects to apply these
principles and brainstorm for breakthrough concept for your productss.
• Arrange for independent
design studies to pursue breakthrough concepts.
How to reduce Quality Costs by Design
The Cost of Quality
The second most effective cost reduction opportunity is designing products for
the minimum quality costs. Unfortunately, in most companies, this “falls below
the radar” because quality costs are not quantified.
The article on
How to reduce
Cost of Quality
opens with a quote from Chuck Cox, Master Six-Sigma
Black-Belt from the George Group: “If you haven't been doing ongoing
continuous improvement, then you can expect that your Cost of Quality will be
between 20% and 35% of the revenue stream or the product’s selling price.”
For military/government contracts the figure could be 45%.
Often, the dollar value of the Cost of Quality is so high that managers don’t
believe it. So Cost of Quality should be one of the first “cost drivers” to be
quantified by Total Cost quantification initiatives.
Cost of quality categories include:
• Factory quality costs for: Rework, Diagnostics, Reinspection of
rework, Scrap, Value of replacement materials and parts, Purchasing actions
to procure replacements materials/parts, Analysis of quality problems,
Planning and corrective actions, Supplier corrective actions, Change-induced
quality costs, Setup change scrap/rework until first good part,
Sorting/screening out sub-optimal merchandise, Inventory carrying costs for
extra inventory caused by quality problems, Discounting sub-optimal
merchandise, and Change orders to correction quality problems.
• Field failure and reliability costs for: Dealing with customer
complaints, Refund/compensation/allowance costs, Returned goods, Warranty
costs, Recalls, Retrofits, Patches, Penalties, Liability costs, Loss of
Goodwill, Reputation degradation, Damage control costs, and Lost sales.
How to Develop Products to Minimize the Cost of Quality
The article: How to Assure Quality by
Design presents many ways that product development can minimize the
cost of quality, in addition to providing a higher-quality product that will
increase sales. Design methodologies include:
• Observe Quality and Reliability Design Guidelines that are in Chapter 10,
A Design for Quality, in the book Design for
Manufacturability & Concurrent Engineering.
• Understand past quality problems by studying lessons learned and
developing proactive plans to avoid costly problems in new designs.
•
Raise and resolve issues early by: learning from past quality
problems; early research, experiments, and models; generate plan-B
contingency plans; and proactively devising and implementing plans to
resolve all issues early.
• Use Multi-functional teamwork. Break down the walls between
departments with multi-functional design teams (Deming's 9th point) to
ensure that all quality issues are raised and resolved early and that
quality is indeed treated as a primary design goal.
• Utilize Quality Function Deployment (QFD) to define products to
capture the voice of the customer the first time without the cost and risk
of changing the design during product development, which increases
development expenses and cause either development delays or encourage
"cutting corners."
• Do Thorough Up-Front Work (a key element of Concurrent Engineering)
so product development teams can optimize quality by design.
• Simplify the design
for the fewest parts, interfaces, and process
steps. Elegantly simple designs and uncomplicated processing result in
inherently high quality products.
• Minimize the exponential cumulative effect of part quality and quantity
by specifying high-quality parts and minimizing part count. The figure in the
article on Design for Quality shows that the quality of the product (the first-pass accept
rate) will be (assuming perfect processing) equal to the quality level of
the parts to the exponent of the number of parts! This graph encourage
high-quality parts and fewer of them to maximize quality.
High-quality parts can remove that variable from product development
efforts, thus assuring that achieving the desired functionality will not be
delayed – or incur more cost – because of part quality issues.
• Select the highest quality processing. Automated processing
produces better and more consistent quality than manual labor.
• Optimize tolerances for a
robust design using Taguchi MethodsTM to
ensure the high quality by design.
• Utilize Poka-Yoke principles in product development to prevent mistakes
by design in addition to traditional manufacturing techniques to prevent
incorrect assembly or fabrication.
• Proactively minimizing all types of risk, not just functionality.
For critical applications, use Failure Modes Effects Analysis (FMEA).
• Base Cost Metrics and Compensation on
Total Cost
and the Time to
Stable Production to avoid compromising quality with cheap parts to save A
cost@ or throwing a sub-optimal design over the wall Aon time.@
• Reuse proven designs, parts, modules, software objects, and processes
to minimize risk and assure quality, especially on critical aspects of the
design.
• Document thoroughly and completely with 100% accuracy and completeness.
• Thoroughly design the product right the first time. Use Design for
Manufacturability techniques presented herein to ensure that a quality
product is design right the first time. Having to redo steps adds to product
development expenses and delays the time-to-market.
How to Maximize Manufacturability while Minimizing the
Product Development Expenses and the Costs of Delays, Firefighting, and Change
Orders.
The Traditional Timeline
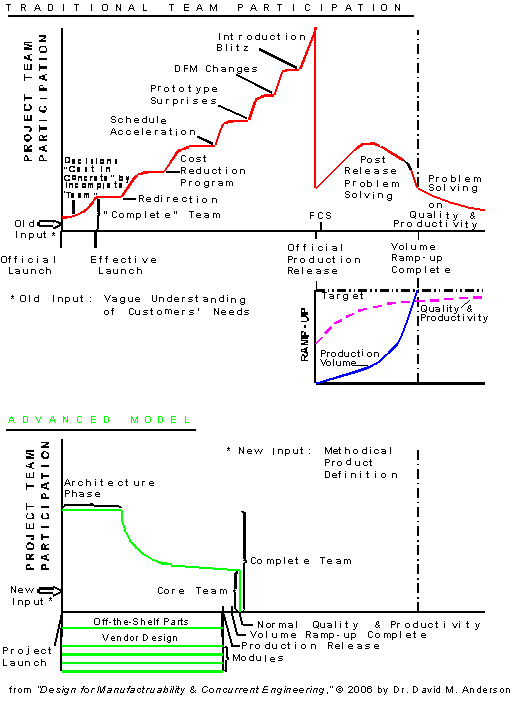
The top graph at the right shows the traditional team participation that
starts with a poor product definition and an incomplete team (usually
missing Manufacturing , Procurement, and Vendors) that makes arbitrary
decisions that soon get “cast in concrete.” These shortcomings and late
consideration of cost and DFM cause many redirections that delay product
development.
But all this lack of thorough up-front work causes a painfully slow ramp-up
(center graph), which causes a lot of post-release problem solving,
firefighting, and change orders (the post-release portion of the top graph).
Even after the volume production has been reached, there is still more
problem solving, firefighting, and change orders to fix quality and
productivity shortcomings.
Unfortunately, when the traditional curve eventually does reach the target
volume, it is late, which may incur penalty costs, overtime charges,
expediting costs, and the cost of lost sales, not to mention the lost
development opportunities when resources are too busy to work on the highest
return products.
The Advanced Timeline
By contrast, in the advanced model (the lower graph), thorough up-front
work not only eliminates the firefighting and change orders, but the
workload drops off after the architecture phase optimizes off-the-shelf part
selection, utilizes previous modules, and brings in vendor/partners s early
to help design the product. The result is the time to stable production (the
only relevant measure of time) occurs in half the time. This also brings in
extra revenue.
Product Development Cost Savings
The areas under the top and bottom curves represents engineer-hours. The
graph shows that the traditional time-line can consume twice the
engineer-hours as the advanced model, which means that product development
expenses can be twice what they should be – or more.
The DFM book and seminars
show dozens of ways to shift from the back-loaded model at the top to the
front-loaded model at the bottom and do the thorough up-front work that
enables the other methodologies presented in this article.
Manufacturability Cost Savings on Worthy
Existing Products
Ensuring that all specialties are working together early allows design
teams to design products for manufacturability by:
• Listening to manufacturing, quality, procurement, and service team members
will raise awareness of manufacturing issues. Applying their knowledge and
experience will help the engineers design for manufacturability.
• Investigating and understanding lessons learned about the
manufacturability of previous or related products. Then create action plans
to do what worked and avoid what didn’t.
• Understand and obey design guidelines. Dozens of these design guidelines
are presented in Chapters 8 and 9 of the book, Design
for Manufacturability & Concurrent Engineering with several presented in
the accompanying article on DFM.
• For printed circuit boards, design rules are well documented. To ensure
manufacturability, obey all design rules for printed circuit boards for:
component placement, spacing, and layout; proper geometries/spacing for
pads, holes, vias, traces, probes, test access, test fixtures, locating
features, and stay-out zones. All components must be automatically placed
and soldered. Lay out circuit boards to ensure testability at the
architecture level, which requires early teamwork with test engineers.
How to Minimize Design Costs with Vendor/Partnerships
The accompanying article Saving Cost
and Time with Vendor/Partnerships shows that using
Vendor/Partnerships to concurrently engineer custom parts will save more
money than sending out for bids on unmanufacturable parts that were designed
in isolation.
This saves cost because vendor/partners thoroughly understand DFM
guidelines, know their process capabilities, and can help company engineers
avoid arbitrary decisions, which unnecessarily raise cost, delay delivery,
and compromise quality. The vendor’s tooling engineer can work with
company engineers to design for tooling that will cost the least and produce
the highest quality parts.
Further, vendor/partnerships benefit from learning relationships
where the customer and vendor learn from each other, thus making each job
better, faster, and less expensive.
• Vendor/partners will provide the lowest total cost because
interacting directly with the customer’s team results in vendors:
• thoroughly understanding the challenges and issues
• making “what if” suggestions early that will maximize
manufacturability
• working with customers early to minimize total cost
Vendor/Partners will not have to add a “cushion” to deal with unknown
customers or unfamiliar designs.
Vendor/Partnerships also avoid the cost of delays and change orders to fix
unmanufacturable designs that were “thrown over the wall.”
How to Minimize Supply Chain and Material Overhead Costs by
Design
• Availability. Designing in readily available parts and materials
eliminates the effort to find replacements or the cost to write change order
or the cost to buy up a lifetime supply of parts that are going out of
production. It also eliminates expediting shipments of parts, materials, or
products and limits the cost of misses sales caused by shortages. This
benefit is enabled by the shifting purchasing agents from
managing bidding wars
to helping teams select parts for the best availability.
• Standardization. Designing around standard parts lowers part cost
and leads to better purchasing leverage and economy-of-scale savings. It
also lowers these overhead costs:
• Material overhead that can be 1/10 of non-standard parts,
which reflects savings in purchasing efforts and encourages engineers to
specify standard parts, thus lowering total cost.
• Standardization results in few parts to order and stock, thus
resulting in less materiel overhead cost and less inventory carrying
costs.
• Standardization results in less expediting and fewer change orders to
solve availability problems
• Deliveries can be faster, more frequent, more dependable, and less
affected by shortages.
• More efficient internal distribution – for fewer parts – with
dock-to-line deliveries possible
• Inventory. Inventory carrying costs can be eliminated by
designing for build-to-order with
concurrently engineered flexible processes, thus saving about 25% of the
inventory value per year!
• Customization. Products and processing can be designed for
cost-effective Mass Customization
to replace expensive “customization by firedrill.”
• Off-the-Shelf Parts offer much potential to ensure part
availability, free resources from designing redundant equivalents, lower
product development expenses, and lowers costs of design, documentation,
prototyping, testing, and the overhead cost of purchasing all the
constituent parts.
However, off-the-shelf must be selected first before arbitrary decisions
preclude their use. The paradox of product development is that:
Designers may have to choose the off-the-shelf parts
first
and then literally design the rest of the product around them.
New section at end of Cost
Reduction article:
What to
Do About Existing Products that Cost Too Much
These are the general principles. Pass
around this article or URL to educate and stimulate interest
In customized seminars and
webinars, these principles are presented in the context of your
company amongst designers implementers, and managers, who can all discuss
feasibility and, at least, explore possible implementation steps
In customized workshops, brainstorming sessions
apply these methodologies to your most relevant products, operations, and supply
chains.
The very first step may be to start with a few hours of the
DFM thought-leader to help formulate strategies and implementation planning.
See his consulting page: http://design4manufacturability.com/Consulting.htm
If you want to discuss Concept Cost
Breakthroughs by phone ot e-mail, fill out this form:
For more information, call Dr. Anderson at 1-805-924-0100
or e-mail him at
anderson@build-to-order-consulting.com.
To explore the opportunities of these techniques at your company call or email
with your
name, title, company, phone, types of products, and needs/opportunities
copyright © 2021 by
David M. Anderson
Book-length web-site on Half Cost Products:
www.HalfCostProducts.com
[DFM Consulting]
[DFM
Seminars] [DFM webinar]
[DFM Books] [Credentials] [Articles]
[Clients] [Site Map]
[DFM article]
[Half Cost Products site] [Standardization
article] [Mass Customization article]
[BTO article] [Rationalization
article]
|